
何为精益生产呢?我们先从定义开始吧。精益生产(Lean Production)是一种持续改进的哲学,其目标是减少生产过程中的周期时间(或交付时间, Lead Time)。这里所说的周期时间,不只是指生产本身,还包括各个工序之间的停滞时间以及在仓储期间的空闲时间。
从根本上说,周期时间和生产效率息息相关,能有效减少周期时间的企业往往能显著提高生产率。这不但是指更高的产品质量、更低的成本和更大的灵活性,还能给企业带来更大的市场份额和更多客户订单。
然而,有些人在网上查找精益生产的定义时,可能会看到“精益生产就是管理层裁员”的说法,这种误解忽略了精益生产的本质——它实际上是一种增长战略。通过减少周期时间,企业可以接到更多订单,从而需要制造更多产品,精益不只不会裁员,反而需要增加员工来应对需求的增加。
精益生产:名字的由来和背后的故事
精益一词究竟是由谁命名的?很可惜,知道答案的人不多,因为很多人都误以为是《改变世界的机器》的作者詹姆斯·沃马克和丹尼尔·T·琼斯。而事实上,这个词的出现还要更早一点点。
“精益生产”一词是由一个美国商人约翰·克拉夫西克(John Krafcik)在1988年他的文章《精益生产系统的胜利》(Triumph of the Lean Production System)中提出的,不过,精益一词确是在《改变世界的机器》一书出版后才真正为大众所熟识的。
《改变世界的机器:精益生产的故事》这本书由詹姆斯·沃马克、丹尼尔·罗斯和丹尼尔·T·琼斯等人所撰写。作者们将“精益生产”用于描述丰田生产方式,而这种生产方式在20世纪50年代诞生,曾为丰田以及其他日本汽车企业带来了显著的繁荣。在此之前,西方世界对丰田生产方式几乎不甚了解,而“精益生产”也从此正式进入了人们的视野。

精益管理:精益生产的延伸
有时候我们会看到这样的说法:精益生产是精益管理的一个子领域。从某种意义上来说,这没错,因为精益管理涵盖了整个组织,以实现整体的优化过程。正因如此,精益管理已经成为多年来企业管理中的一项原则。
需要注意的是,精益管理其实是由精益生产演变而来的,而不是相反。除此之外,还有一些专门的领域,例如精益行政管理和精益会计,这些也都是为了优化特定领域的流程。而“精益制造”这一常见的称谓,其实也只是精益生产的同义词而已。
Kaizen——精益生产的基本理念
精益生产的基本哲学是一种持续改进,这一理念源自日本传统的“Kaizen”(改善)概念。Kaizen由“改变”(Kai)和“更好”(Zen)两个日语词汇组成,意味着改进永远是一个没有终点的过程。换句话说,企业永远不应满足于现状,而应不断追求新的目标。
这也是一种积极的企业文化,意味着所有的过程环节都是值得改进的。瑞典企业家简·卡尔森曾精辟地总结道:“你不可能将一件事提高1000%,但你可以把1000件小事各提高1%。”
Kaizen和持续改进过程(CIP)的区别
Kaizen这种理念已成为全球生产活动的标准部分,它的现代化体现就是持续改进过程(CIP)。简单来说,Kaizen是一种根本性的态度,而CIP则是一种具体的精益生产方法。CIP的核心是反复进行的PDCA或者DMAIC循环。
通过PDCA或者DMAIC循环,企业可以像进行实验一样,提出假设并加以验证,如果验证结果正确,改进措施就会成为新的标准。这也表明,员工自主实施的改进,是持续改进过程中的重要一环。
精益生产与工厂设备的实现
在实施精益生产时,员工不只需要得到充分的培训和相关技能,还需要提供正确的设备。例如,借助“精益生产组装系统”,企业可以轻松地创建运输推车、货架等用于精益流程的设备。公司最好为生产车间设立专门的CIP车间,以便不断进行改进。在这个过程中,错误和失误是可以容忍的,正是这些小的改进,构成了CIP整体的重要基石。
精益生产中的“浪费”及其解决方法
前面提到过,精益生产的目标是减少周期时间,那么就必须识别出那些导致周期时间增加的因素,并尽量减少它们。丰田生产方式的创始人大野耐一就曾强调:“我们所做的就是观察从客户下订单到收到货款的时间线,并通过减少不增值的浪费来缩短这条时间线。”在精益生产中,有三个关键的概念用于描述浪费:Muda(浪费)、Mura(不平衡)和Muri(过载)。其中,Muda最为人们所熟知,它指的是生产过程中所有不增值的活动。
精益生产中的“七种浪费”分别是:
- 材料的多余移动:材料的移动虽然需要资源,但并不会增加任何价值,而且在搬运过程中还可能造成损坏。解决方案:尽量使工作站靠近,并使各工序之间实现同步和联动。
- 高库存水平:仓库过满通常反映出计划不合理以及对物料需求量的认知不足。解决方案:稳定并标准化流程。
- 不符合人体工学的动作:不符合人体工学的工作台设计可能会导致员工处于尴尬的工作姿势,进而影响健康和工作效率。解决方案:采用人体工学原则设计工作台系统。
- 可避免的等待时间:等待时间无法完全消除,但应尽量减少。解决方案:使员工能够承担多种岗位职责以充分利用其工作能力。
- 过度生产:由于错误评估了需求,导致产品滞销,资本长期被占用。解决方案:引入拉动原则,使生产链与客户的需求节奏保持同步。
- 过于复杂的流程:那些过时或不必要复杂的流程,同样会造成浪费。解决方案:持续改进公司流程,简化生产设计。
- 次品与返工:当生产出现错误时,要么产品完全无法使用,要么需要重新加工。解决方案:通过应用Poka-Yoke原则防错,并利用5S方法来优化工作台,提升产品质量。
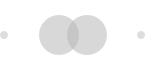
拉动原则与精益生产的价值
避免浪费是精益生产的一大优势,而这与提高增值和谨慎使用生产资源是密不可分的。拉动原则就是一个很好的例子,它通过以订单为基础来推动生产,有效地避免了因过度生产和库存而产生的浪费。相比传统的推动式生产,拉动原则能够大大缩短周期时间并提高灵活性。举例来说,最初的拉动管理是通过看板系统来实现的,客户订单触发生产过程,各生产单元根据下一个单元的需求进行生产,从而实现“按需生产”,而不是“按预测生产”。最终,生产链中的各个环节就会实现最大程度的协同,这种优化不仅体现在库存水平和周期时间的减少上,更表现在整个生产过程中无中间缓冲的“一件流”生产上。
热门跟贴